용접 결함과 예방 조치 - Part 1 포스팅에 이어 용접 불연속(Weld discontinuities)의 종류에 대하여 알아보겠습니다.
Weld Discontinuities
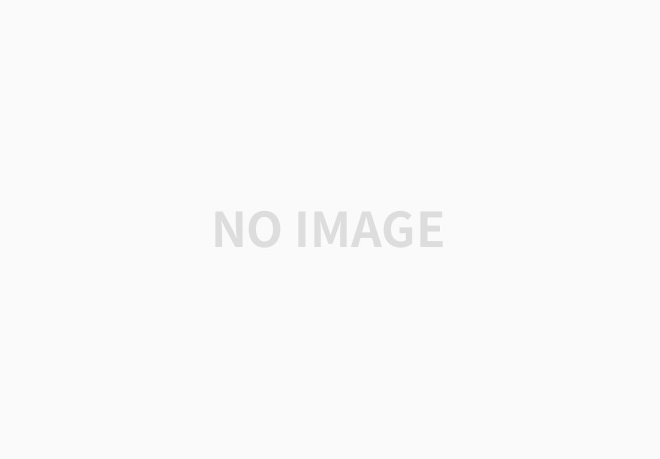
그림 9. 기공 (POROSITY: PIT)
정의: 응고 도중에 갇힌 가스에 의해 형성된 구멍 형태의 불연속
주요 원인:
1. 용접되는 조인트에서의 녹, 오일, 페인트, 습기와 모재의 높은 황(Sulfur) 함량
2. 용접봉 피복의 습기(SMAW), 플럭스의 습기(SAW), 보호가스에서의 습기(GMAW)
3. 매우 적은 보호 가스(GMAW)나 쌓인 플럭스 높이 (SAW)
4. 강한 바람 (SMAW, GMAW)
5. 매우 높은 용접 전류, 아크 길이, 아크 전압
예방 조치:
1. 용접되는 조인트의 청결 유지
2. 용접봉 재 건조(SMAW), 플럭스 재 건조(SAW), 그리고 적절한 보호가스 사용(GMAW)
3. 적절한 양의 보호가스 사용(GMAW), 적절한 높이의 플럭스 사용(SAW)
4. 바람 차단막 설치 (SMAW, GMAW)
5. 적합한 용접 전류, 아크 길이, 아크 전압을 사용
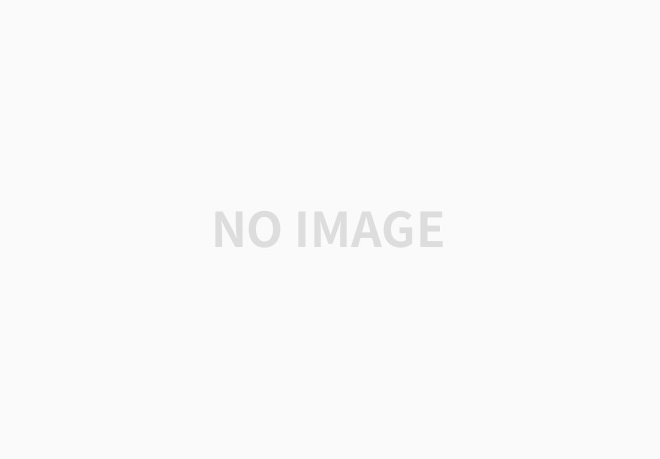
그림 10. 기공 (POROSITY: BLOWHOLE)
→ 그림 9의 PIT 기공은 원형이 형태라면 BLOWHOLE 기공은 길쭉한 타원형의 기공 형태
→ 그림 9의 POROSITY-PIT와 내용 동일
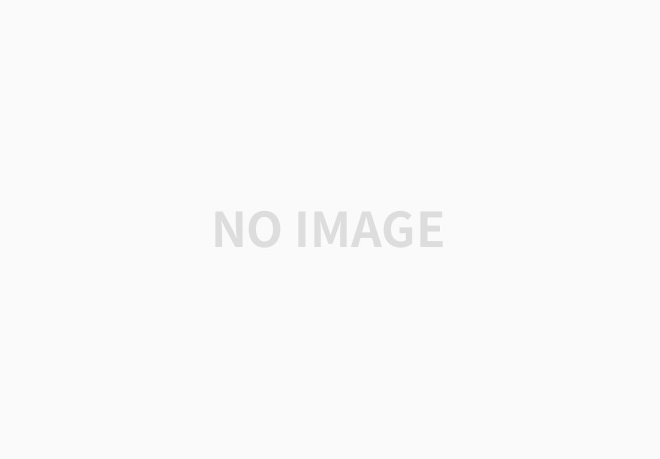
그림 11. 슬래그 혼입(SLAG INCLUSIONS)
정의: 용접부에 비금속의 고형의 물질이 갇힘
주요 원인:
1. 너무 낮은 용접 전류
2. 너무 큰 아크 길이
3. 너무 큰 위빙 폭(Weaving width)
4. 너무 좁은 groove
5. 앞선 layer에 남아 있는 슬래그
6. flat position에서의 welding 방향의 아래로 기울어진 용접 축
예방조치:
1-4. 적합한 용접 변수와 그루브 각도의 사용
5. 앞선 layer의 슬래그를 완전하게 제거
6. 수평으로 용접 축을 위치하는 것을 유지
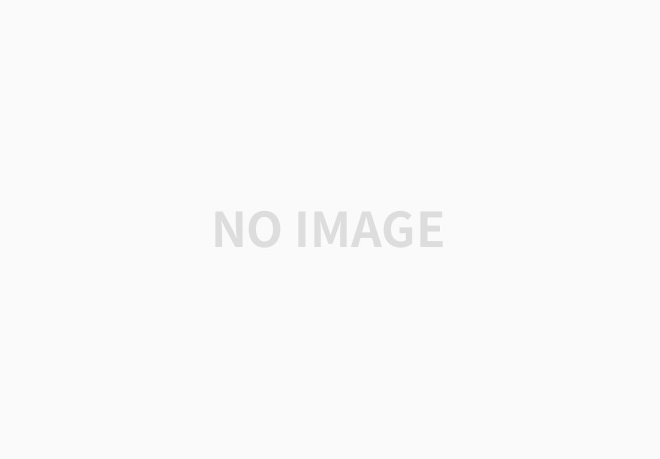
그림 12. 융합 불량 (INCOMPLETE FUSION)
정의: Weld metal과 joint fusion face 사이에서의 또는 인접한 weld beads 사이에서의 융합이 되지 않은 용접 불연속
주요 원인:
1. 너무 낮은 용접 전류
2. 너무 빠르거나 느린 용접봉 조작
3. 너무 길거나 짧은 아크 길이나 아크 전압
4. 너무 좁은 welding groove
예방 조치:
1. 적합한 용접 변수 사용과 groove angel
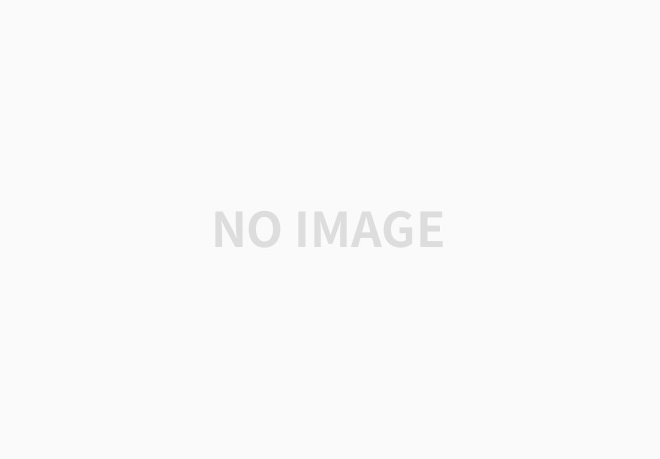
그림 13. 용입 부족(INCOMPLETE JOINT PENETRATION)
정의: 용접 조인트의 두께보다 작게 불완전하게 용입
주요 원인:
1. 너무 좁은 welding groove
2. 너무 낮은 용접 전류
3. 너무 긴 아크 길이나 아크 전압
4. 너무 빠르거나 너무 느린 용접봉 조작
예방 조치:
1. 적절한 groove 구성의 사용
2-4 적합한 용접 전류, 아크 길이나 아크 전압의 사용, 용접봉 조작
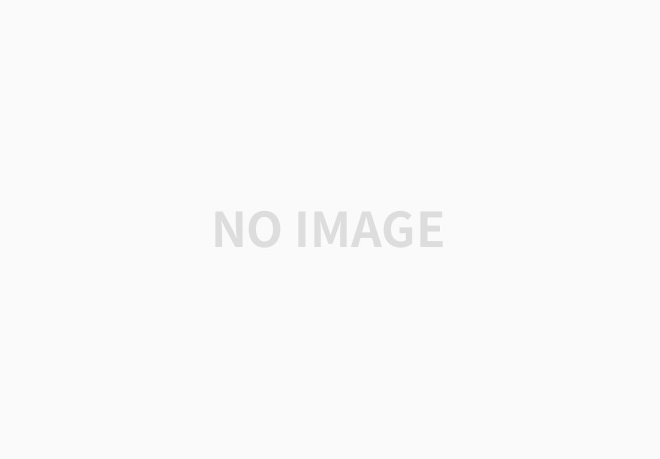
그림 14. 용락(EXCESSIVE MELT-THROUGH: BURN-THROUGH)
정의: 주로 root pass에 발생하며 과도한 용략으로 용접 비드에 구멍이 발생함
주요 원인:
1. 너무 큰 루트 간격
2. 너무 높은 용접 전류
예방 조치
1. 적합한 루트 간격과 용접 전류
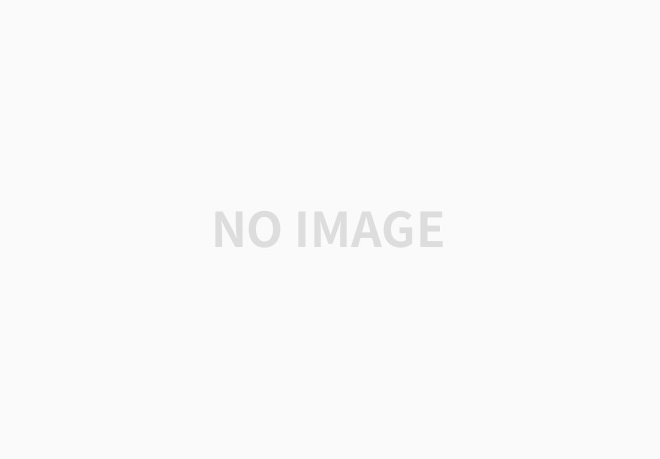
그림 15. 냉간 균열(COLD CRACK: ROOT CRACK, TOE CRACK, UNDERBEAD CRACK, TRANSVERSE CRACK)
정의: Steel이 대략 200도보다 낮은 온도에서 용접 금속의 응고가 완료된 후 발전하는 크랙
주요 원인:
1. 용접부에서의 확산하는 수소
2. 용접에서의 취성 구조(brittle structure)
3. 용접부에서의 구속 응력(restraint stress)
예방 조치:
1. 용접봉 재 건조(SMAW), 플럭스 재 건조(SAW)
2. 모재 예열
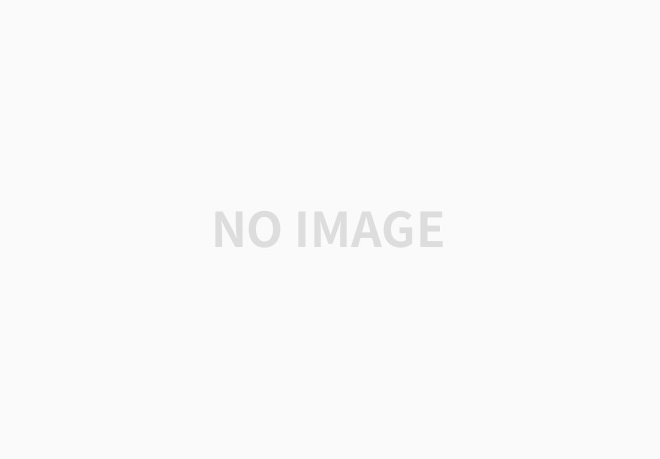
그림 16. COLD CRACK (LAMELLAR TEAR)
정의: 수축 응력이 기본적으로 판 두께 방향으로 가해지면서 발생하는 균열로서 표면 아래에서 형성되며 계단 형태로 판면에 평행합니다.
주요 원인:
1. 두께 방향으로의 모재의 부적합한 연성
2. 모재에서의 높은 황 함량
3. 모재에서의 비금속 개재물(Nonmetallic inclusions)
4. 용접부에서의 수소
5. 모재의 두께 방향으로의 인장 응력
예방 조치:
1-3. 두께 방향으로의 높은 연성을 가지는 모재, 낮은 황, 개재물을 가지는 모재 사용
4. 저수소계 용접봉을 사용
5. 조인트 세부 설계를 수정하고 응력을 감소시키는 용접절차서로 개선
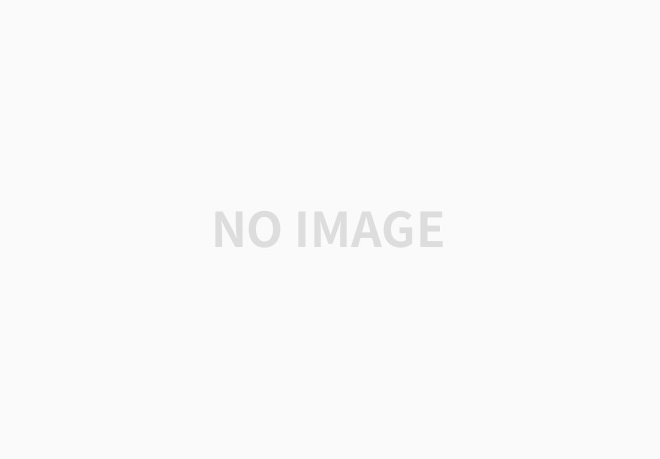
그림 17. HOT CRACK (CRATER CRACK, LONGITUDINAL CRACK, PEAR-SHAPE CRACK , SULFEUR CRACK)
정의: 용접 금속의 응고 중에 발전하는 크랙
주요 원인:
1. 너무 높은 용접 전류
2. 너무 좁은 용접 groove
3. 모재에서의 많은 황(sulfur)
예방 조치:
1. 적절한 용접 전류 사용과 크레이터 처리
2. 적합한 groove angle 사용
3. 용접 전에 welding groove에서의 황 석출(sulfur segregation)을 검사
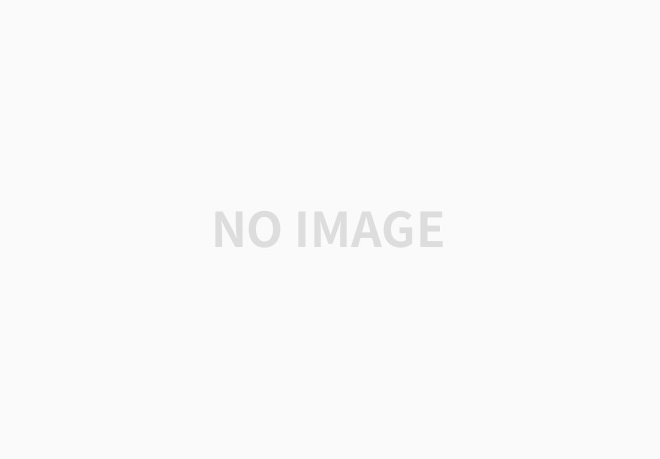
그림 A-1: 용접 결함이 의한 용접에서의 결함 (용접 조인트의 굽힘 시험 결과)
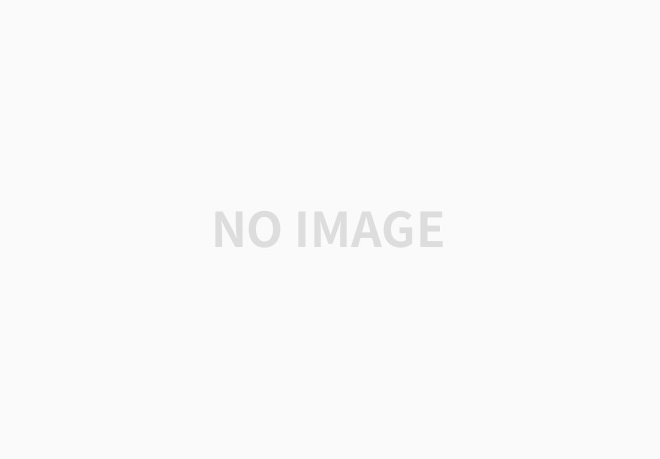
그림 A-2: 용접 결함이 의한 용접에서의 결함 (용접 조인트의 인장 시험 결과)
여기까지 용접 결함 / 용접 결함의 종류 - Part 2를 마칩니다.
'플랜트 > 용접' 카테고리의 다른 글
서스 용접(SUS 용접)의 5가지 중요 문제점 (0) | 2020.06.24 |
---|---|
필렛 용접 각장(Fillet weld leg) / 용접 각목 (Fillet weld throat)이란 ? (0) | 2020.06.23 |
Grade 91 합금 재질의 용접 PART-2 (0) | 2020.06.19 |
용접 결함 / 용접 결함의 종류 - Part 1 (0) | 2020.06.19 |
배관 용접 퍼지(purge) /용접 퍼징(purging) (0) | 2020.06.18 |
댓글